Interview with José Luis García
Spanish Nation Research Council (CSIC), as one of the largest European public research institution with high expertise in the biotechnology field, gives its contribution to BioSFerA on biological processes at laboratory scale thorough its institute, the Center for Biological Research Margarita Salas (CIB) (Madrid). Its main activity is the research of the best microorganisms, playing a key role in the double stage fermentation characterising the BioSFerA process.
Exploring the micro level and the microorganisms’ interaction with the surrounding environment is crucial when moving processes from the laboratory to pilot scale level. Few questions to go deepen the CSIC activity and the biological research in laboratory with José Luis García, Research Professor at CIB (CSIC) and leader of the Environmental Biotechnology group:
As project partner, how CSIC contribute to the project and what is the innovative aspect led by your research activity?
Our main contribution to BioSFerA is to develop a new collection of system metabolic engineering tools that can allow to modify the acetogenic bacteria and the oleaginous yeasts in order to obtain robust bacteria and yeast that could render higher production yields of acetate and lipids than the natural wild type strains. Using these tools and considering the lessons learned during the implementation of the processes at industrial scale it will be possible to propose other modifications to improve even further the production yields.
Your work is focused on bacteria and their interaction with organic matter and the surrounding environment. What are the main limitations hindering bacterial activities to consider for their performance, specifically in the BioSFerA processes?
It’s important to consider the final objective of the process, which in BioSFerA is to transform the syngas obtained from biomass gasification into acetate that will be further used to produce lipids. Analysing our model, we can split it into two main steps: in the first one, we use acetogenic bacteria to transform syngas into acetate, whereas in the second step we use oleaginous yeasts to transform acetate into lipids. To develop an industrial efficient process the first problem that we have to handle is how to increase the bacterial production of acetate from syngas. This can be achieved by combining the production of enough microbial biomass from syngas and an efficient transformation of syngas into acetate. In addition, we have to take care of possible syngas contaminants that are toxic for the bacterial acetogenic strains and that can affect bacterial growth or viability. Hence, we have performed a screening of different acetogenic bacteria that are able to grow at high cell densities, that produce high amounts of acetate, and that are resistant or tolerant to some contaminant/impurities present in syngas.
Example of Y. lipolytica strains growing
on YPD (rich liquid medium) agar plates.
Considering the acetate production, how the syngas composition from the different biomass can affect the fermentation process?
As mentioned above, in BiosFerA we are traying to transform the residual biomass into syngas: a mixture of carbon dioxide, carbon monoxide and hydrogen, that is obtained by a process named gasification. The syngas, as result of a gasification process, depends on the origin and properties of the biomass which influence the presence of the contaminants and the syngas composition. Usually, the biomass gasification not only produces syngas, but also other compounds like hydrogen sulphide, hydrogen cyanide, benzene, ammonia, methane, etc. This means the production of acetate will be affected by the proportion of the main gases (CO2, CO, H2), that varies depending of the biomass and the gasification conditions and that are responsible of the bacterial growth and the acetate yields, and also by the presence of toxic unwanted contaminants. Therefore, it is important to find the most appropriated syngas composition as well as to eliminate as much as possible the unwanted contaminants to a level that can not affect bacterial growth or acetate production.
What kind of approach have you followed in these research activities and how is the work coordinated with the other partners? What are the advantages of having such a broad, interdisciplinary team as BioSFerA?
In a very early steps, we have collected all the information available in the literature dealing with the metabolism, molecular biology and processes of the organisms of interest, this is acetogenic bacteria and oleaginous yeasts. Then, we have selected the best strains and performed a screening of their properties using different culture conditions in order to test which are the best acetate producers from syngas and lipid producer from acetate. After selecting the best performing microorganisms, i.e. the acetogenic bacteria Moorella thermoacetica and the oleaginous yeast Yarrowia lipolytica, we have used systems metabolic engineering approaches to identify the target genes that have to be deleted or overexpressed, to channelling the metabolism to the production of the metabolite of interest. After modifying the strains, they have been initially tested at CIB-CSIC at lab scale using shake flask cultures and then transferred to CARTIF and BBEPP for fermentations in bioreactors at high volume levels. At this point, the interdisciplinary nature of the different groups involved in BioSFerA project allows us to find the best operational conditions to produce the compounds of interest at pilot and industrial scales.
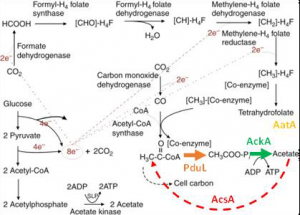
Acetate metabolism in acetogenic bacteria.
Target genes are indicated in colours.
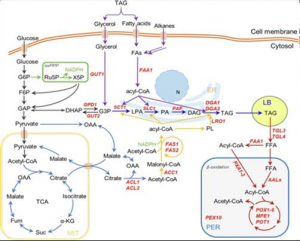
Lipid (TAG) metabolism in oleaginous yeasts.
The main target genes are indicated in red.
So, first you analyse the organism’s metabolism to identify the best strains and then you guide them in the metabolic process of the desired substances, through genetic modifications. What is the value added to use GMO microorganisms?
GMO microorganisms are designed for different purposes, but in principle they are all aimed at increasing the performance of processes. The yield of the process can be increased by redirecting the carbon flux to the production of the desired product and at the same time by avoiding the formation of unwanted by-products. Additionally, as it is the case of lipids, we can also modify the microorganism eliminating the degradative pathways of lipids and fatty acids, facilitating that the decided final product is accumulated inside the cell, without the possibility of its further degradation. The GMOs constructed in BiosFerA project are oriented to increase the production of acetate from syngas in the case of acetogenic bacteria, and to increase the production of lipids from acetate in the case of oleaginous yeast. If required, the strains can be also modified to acquire other properties, for instance the resistance or tolerance to specific toxic contaminants.
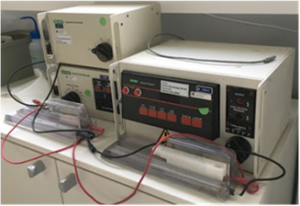
Electroporator used to create OGMs
Detailed information on the biological research at laboratory scale carried out by the BioSFerA’s partners are available in the Deliverable 3.2 – Deliverable 3.3.
Further explore through the opinion-Editorial Letter by CSIC – Integrating greenhouse gas capture and C1 biotechnology: a key challenge for circular economy.